The Mark II Upgrade – A Boost for THP Capacity
Upgrade to Cambi’s Mark II system for enhanced thermal hydrolysis performance, improved reliability, and reduced maintenance.
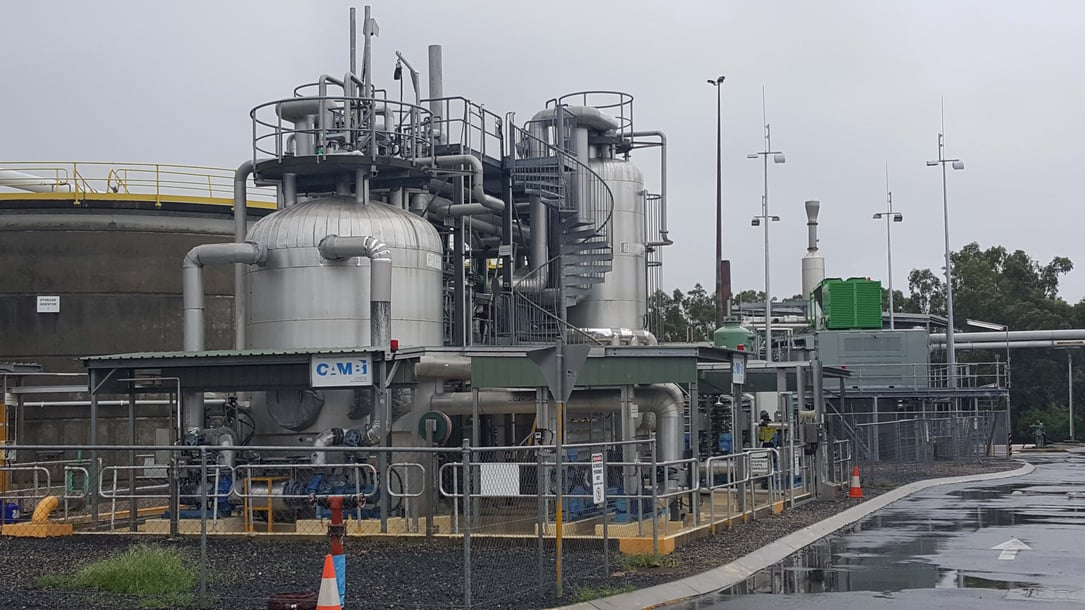
newsletter
As Cambi incessantly develops thermal hydrolysis process (THP) technology while servicing a diverse client base, it has built expertise in the continuous improvement of the machinery and even the ancillary equipment in the market it works best with. This has fostered, over time, new THP models like model E which has a focus on energy efficiency, and a notable array of upgrades, like the pulper upgrade and the Flexishaft pump conversion. One of these upgrades, which brings older Cambi systems up to the standard of current plants, is called the Mark II upgrade.
All Cambi THP systems delivered today are Mark II systems. Though Mark I systems have great performance and reliability, older Cambi systems would benefit greatly from an upgrade in that it modernizes the system and increases hydraulic capacity.
What Does a Mark II Upgrade for a THP Plant Entail?
Simply put, a Cambi Mark II upgrade is the modification of the Cambi system to increase throughput capacity and overall performance, specifically achieving a higher degree of sludge breakdown or disintegration compared to Mark I systems.
Mark I systems that are upgraded to Mark II typically augment capacity up to 30%, which can be crucial for plants planning to increase sludge intake.
The main changes that achieve Mark II status include the following:
- Direct blowdown from the reactor to the flash tank. In Mark I systems, this step occurs with prior depressurization from the reactor to the pulper. This results in a high-pressure blowdown which increases the disintegration of the sludge. Removing depressurization also reduces cycle time in the reactors.
- Removal of the radioactive level switches in the reactors, replaced by conventional flow transmitters.
- Reducing overall reactor cycle time, which leads to increase in system capacity
- Optimized steam injection step
- Modernization of the control system. This assures that the thermal hydrolysis plant is efficient, reliable and safe for the years to come.
Below is the change in the reactor cycle time expected with a Mark II upgrade:
|
Mark I |
Mark II |
Sludge filling time (sludge filling the reactor) |
15 minutes |
10 minutes |
Steam filling time (steam boiler injecting steam into the system) |
15 minutes |
10 minutes |
Retention time |
30 minutes |
30 minutes |
Steam flash into the pulper (depressurization step) |
15 minutes |
Not needed |
Sludge flash into the flash tank |
15 minutes |
10 minutes |
TOTAL |
90 minutes |
60 minutes |
Planning and Execution of a Mark II Upgrade: What to Expect?
For a THP plant that may be interested in this upgrade, they can expect the following activities to achieve the changes mentioned above:
- Introduction of internal equipment for the reactor
- Modification of the pulper steam injection configuration
- Modification of steam injection to the reactors
- Modification of piping to ventilate process gases
- Updating the programmable logic controller (PLC) and the human-machine interface (HMI) logic.
To display the concrete impact of a Mark II upgrade, a Cambi plant in Australia shared the effect on their capacity before and after the modifications.
The Mark II Upgrade of Oxley Creek, Australia
The Oxley Creek sewage treatment plant in Brisbane is the first Cambi THP site in Australia. It is Brisbane’s second-largest wastewater facility and is now operated by Queensland Urban Utilities (QUU). The facility processes both sludge produced on-site and imported sludge from surrounding areas. In this particular plant, waste-activated sludge or secondary solids are treated by a Cambi B12 system to produce biosolids for land application. Construction of the THP unit for the facility began in 2005 and the system was commissioned on-site in 2007.
The Cambi THP system at Oxley Creek during its handover in 2007
Before the upgrade, the plant serviced a population equivalent of about 310,000. Biogas produced at the plant is transformed into electricity, covering a significant portion of the site’s total electricity demand. Natural gas covers the rest of the plant's energy consumption.
Over a decade after commissioning, in 2018, QUU examined the prospect of increasing import capacity for Oxley Creek. This would increase biogas production and, therefore, reduce energy costs. There were a few ways the site could achieve this with THP, namely, add a fourth THP reactor, upgrade the system to Mark II, or do both. A Mark II upgrade was assessed as the best route for the plant, with the following targets:
- Increase sludge treatment capacity from 280 to 400 m3/day, representing about 44 tonnes of dry solids (tDS/day) to 64 tDS/day
- Improve energy efficiency, targeting the pulper operating temperature to be between 80 and 100°C
- Improve maintainability and operability by replacing certain parts
It was decided that Cambi would oversee the manufacturing and delivery of all the systems relevant to the upgrade except for piping modifications, which were done by a local company, while Cambi remained responsible for testing the work.
The Mark II upgrade for Oxley Creek had the following timeline, with installation and commissioning including the alterations accomplished by the local partner.
Period |
Activity |
March 2018 |
Project kick-off |
2018 |
Manufacturing and delivery |
December 2018 – February 2019 |
On-site construction for mechanical and system upgrade (installation, commissioning, including non-Cambi scope) |
February – March 2019 |
Performance testing |
The upgraded plant achieved the target goals of the project, with remarkable outcomes:
- CAPACITY: A throughput increase of approximately 43%. During the testing period, an average capacity of 394 m3/day was observed. QUU can take this further to 450 m3/day if they also decide to upgrade some ancillary equipment.
- ENERGY EFFICIENCY: Steam consumption was reduced by 13%, reducing expenses for natural gas usage at the site and helping QUU lower carbon emissions.
Effects of the Mark II upgrade on THP capacity and natural gas usage at Oxley Creek.
Capacity is represented by the blue graph (cubic meter averages per day) while natural gas is represented by the green line (Gigajoules per kiloliter).
The figure excludes additional natural gas usage during installation and feed flow outliers for clarity.
As Cambi brings its client base into the next few decades, Mark II upgrades for older systems may be more common given its proven effect on capacity and efficiency. As of January 2024, the Cambi THP plant in Whitlingham, Norwich, in the United Kingdom, has signed on to shift to Mark II.
Want to learn about other upgrades that can be made to enhance the performance of a Cambi system? Get in touch with our Services team by sending a message via our contact page with the topic “customer support.”
Agnieszka leads the upgrades of Cambi THP systems around the globe as an integral part of the Services team.
The Carbon Footprint of Wastewater Treatment Plants
Discover how wastewater treatment plants can reduce their carbon footprint through smart technologies and innovative sludge management practices.
Dive inSludge Gasification: Fundamentals and Integration Scenarios
Learn about sludge gasification – an energy-focused endpoint for sludge, and various implementation approaches.
Dive inSludge Pyrolysis: Exploring Benefits and Limitations
Discover how wastewater utilities are using thermal processes like sludge pyrolysis to reduce waste volume and eliminate harmful contaminants efficiently.
Dive inUrban Wastewater Treatment Directive: A Guide for EU Utilities
The 2024 UWWTD revision brings stricter standards, new deadlines, and big shifts for Europe's wastewater sector. Here's what utilities need to know.
Dive in